动态提取罐可用于中药、食品、化工行业的常压、微压、水煎、温浸、热回流、强制循环、渗漉、芳香油提取及有机溶媒的回收等多种工艺操作。罐体配备 CIP 清洗自动旋转喷洗球头,测温孔、防爆视孔灯、视镜、快开式投料口等,确保操作简便,符合 GMP 标准。设备内筒体材质为进口 SUS304 ,夹套采用全封闭硅酸铝毯保温,外筒体贴 SUS304 亚光薄钢板饰面。设备成套供应包括:除沫器、冷凝器、冷却器、油水分离器、过滤器、气缸、控制台等附件
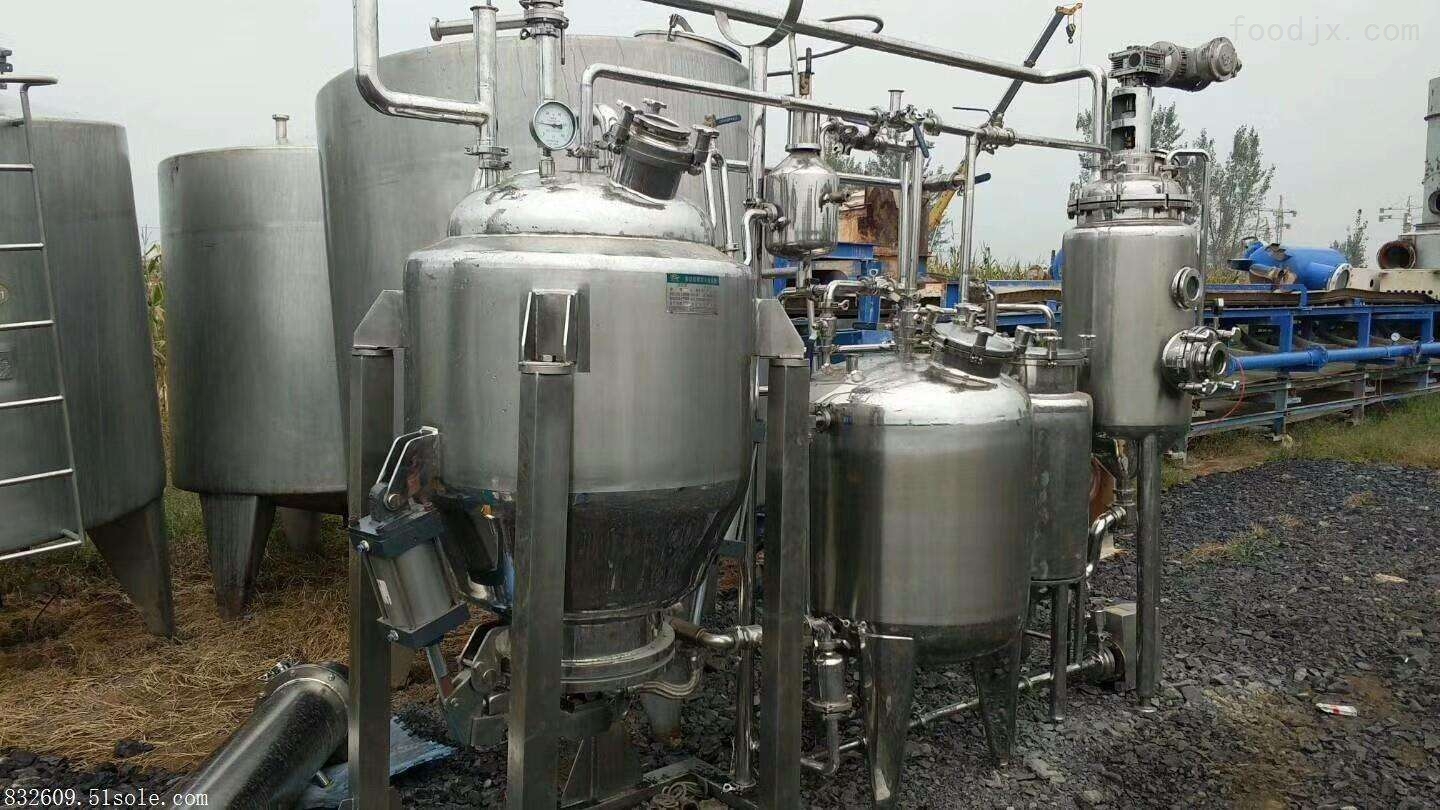
1设备特性
动态提取罐的设备特性:
1、传统型式,所占建筑空间较小,为提取车间广泛使用。
2、出渣门上设有底部加热,使药材提取更加*。
3、改进出液方式和增加搅拌装置后可应用于动态提取系统。
2工艺参数
规格------型号 |
TQA-1 |
TQA-2 |
TQA-3 |
TQA-6 |
TQA-8 |
TQA-10 |
容积L |
1200 |
2300 |
3200 |
6300 |
8500 |
11000 |
罐内设计压力Mpa |
0.09Mpa |
|||||
夹层设计压力Mpa |
0.3Mpa |
|||||
加料口直径mm |
400 |
400 |
400 |
500 |
500 |
500 |
加热面积m^2 |
3 |
4.7 |
6.8 |
10 |
12 |
15 |
冷凝面积m^2 |
4 |
5.4 |
9.0 |
10 |
15 |
18 |
冷却面积m^2 |
1 |
1 |
1 |
2.2 |
2.2 |
2.2 |
过滤面积m^2 |
0.30 |
0.30 |
0.30 |
0.30 |
0.30 |
0.36 |
排渣门直径mm |
800 |
800 |
800 |
1000 |
1000 |
1000 |
耗汽kg/h |
285 |
346 |
570 |
718 |
903 |
1140 |
设备重量kg |
1800 |
2050 |
2400 |
3025 |
4030 |
6500 |
加热汽管口 |
DN-50 |
DN-50 |
DN-65 |
DN-65 |
DN-80 |
DN-80 |
二次汽管口 |
DN-80 |
DN-80 |
DN-100 |
DN-100 |
DN-100 |
DN-100 |
冷却水管口 |
DN-50 |
DN-50 |
DN-65 |
DN-65 |
DN-70 |
DN-70 |
电动机功率kw |
2 |
3 |
4 |
5.5 |
7.5 |
7.5 |
搅拌转速 |
21 |
21 |
32 |
32 |
32 |
32 |
3工作原理
将药材投入提取罐内,加药材的5~10倍的溶媒如水、乙醇、甲醇、丙酮等(据工艺要求)。开启提取罐直通和夹套蒸汽阀门,使提取液加热至沸腾20~30分钟后,用抽滤管将1/3提取液抽入浓缩器。关闭提取罐直通和夹套蒸汽、开启加热器阀门使液料进行浓缩。浓缩时产生二次蒸汽,通过蒸汽发器上升管送入提取罐作提取的热源和溶液,维持提取罐内沸腾。 二次蒸汽继续上升,经冷凝器冷凝成热冷凝液,回落到提取罐内作新溶剂加到药面上,新溶剂由上而下高速通过药材层到提取罐底这样形成的新溶剂大回流提取,故药材中溶质密度与溶剂中含溶质密度保持高梯度,药材中的溶质高速溶出,直至*溶出(提取液无色),此时,提取液停止抽入浓缩器,浓缩的二次蒸汽转送冷却器,浓缩继续进行,直至浓缩成需要比重(1.2~1.34)的药膏,放出被用。提取罐内的无色液体,可放入贮罐作下批复用,药渣从出渣门排掉,若是用有机溶剂提取,则先加适量的水,开直通和夹套蒸汽,回心溶剂后,将渣排掉。
4膜式提取罐
中药提取,生物医药产品的功效需要以目标提取物的活性为基础保障,传统的提取罐工艺首先要将动植物物质高温蒸发干燥粉碎,然后有机溶剂浸提,高温干燥浓缩成粉,两次高温基本破坏了目标产物的活性,使产品丧失理论功效,开元生物的生物膜提取罐是将动植物物质原浆粉碎,通过超滤膜纳滤膜进行高精度提取,
烟台开元以技术的进步推动工业提纯理论的变革和发展,推动膜提纯浓缩技术从实验室试验技术到产业化应用过度,并成功的实现了工业级,规模化分类提纯制备。以自主创新的形式实现了对广义精确目标提取物有效的,产业化,工业级工艺流程解决方案:x组合多功能生物医药分离提纯机(单机组标准件模块化组合)。
在确保目标提取物的高活性.高纯度.高质量前提下:
以反渗透膜技术对大小在50-400分子量的小分子,酸性,碱性有机溶液的净化分离浓缩;
以纳滤膜技术对200-2000分子量的免疫球蛋白,生物肽,羊胎素,氨基酸,蛋白质.....目标产物;
以超滤膜技术对500-50000分子量的目标产物;
实现广义的精确提取.浓缩.提纯.结晶的工艺研发能力。
相较于传统的动态提取罐.浓缩罐,开元膜式提取罐具有以下特点:
(1)分离过程无相变化
(2)分离过程在常温下进行,尤其适用于热敏物质的分离和浓缩;
(3)仅用压力作为膜的动力,自动化控制,方便维修;
(4)有效面积大,滤速快,分离效率高;
(5)适用范围广,工艺流程短
本文地址: https://www.xsyiq.com/14550.html
网站内容如侵犯了您的权益,请联系我们删除。